
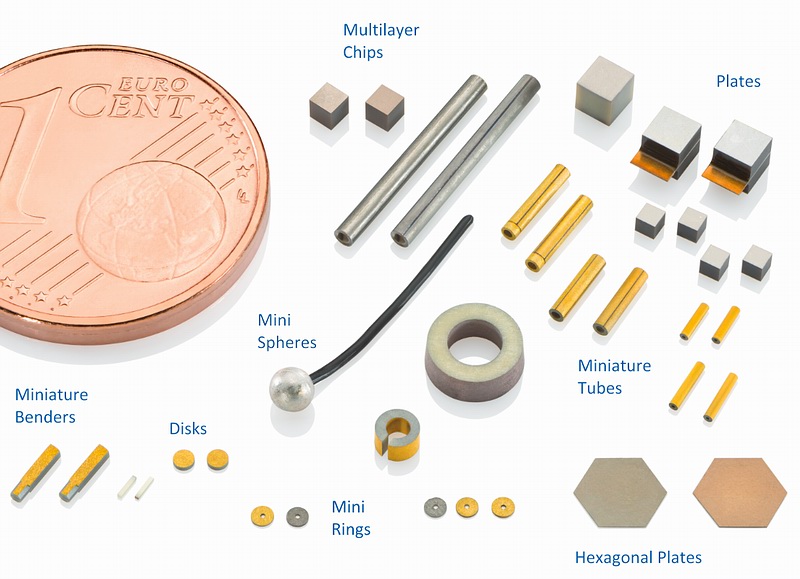
applied voltage.įorce is proportional to applied voltage across the piezo (Figure 3). The displacement remains even if the electrodes are disconnected from the voltage source, except for the small leakage current found with any normal capacitor.įigure 3. Applied voltage does maintain a reasonably proportional relationship with the force generated by the piezo actuator (Figure 3C).Ĭharge on the piezo capacitance holds a good proportional relationship with the displacement over most of the piezo actuator's range of motion. Displacement of the piezo is proportional to the electric field, and the electric field is a function of the electrode voltages and the distance between the electrodes. When voltage is applied to the piezo, the capacitance also changes because the distance between the electrodes is changing (Figure 3A). But in the piezo, C is not constant since the spacing between electrodes changes with applied voltage. Based on its configuration and physical shape, the piezo will change shape as a (DC) voltage is applied across its terminals (Figure 2).Ĭoulomb's law states that Q = CV. Well below resonance, the piezo can be modeled as a simple capacitor. Ultrasonic drilling/welding/knives/scalpels/scalarsĪpplications for operation well below resonance include:.Piezo actuator applications for operation at or near resonance include: Multiple piezos can be used to provide a stronger haptic response and more localized haptic feedback. They can be made into custom shapes for specific applications or packaging constraints, and are offered as single-layer or multilayer structures.
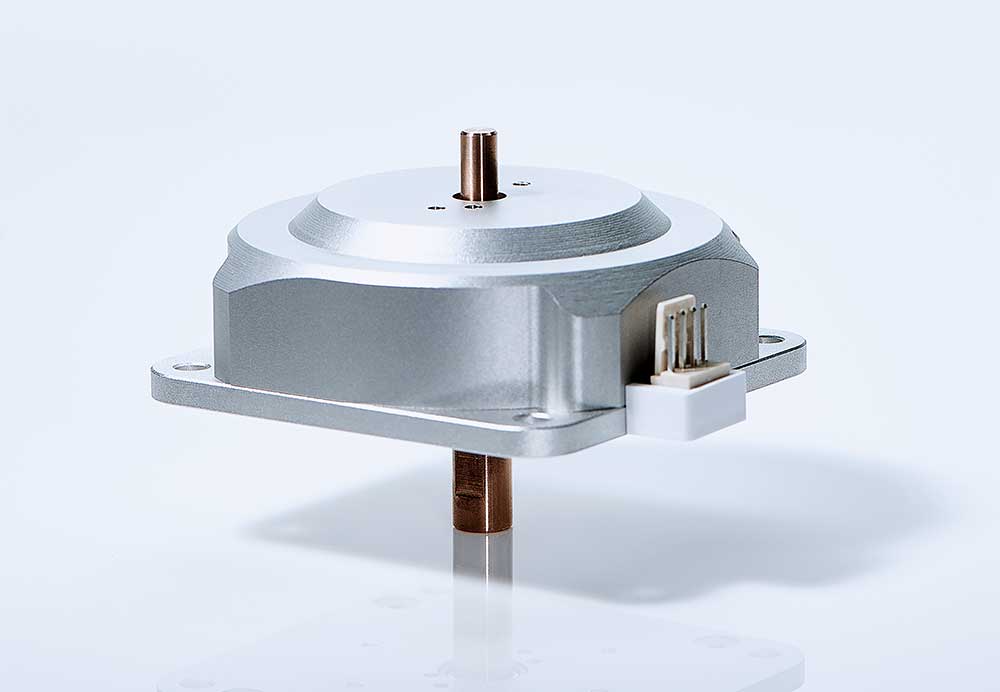
Piezos are available in many different shapes, sizes, thicknesses, voltage ranges, force, and capacitance ratings. Piezo-based haptics offer several advantages including a fast response time, thin profile, low power, and a wide range of available piezo characteristics and mounting techniques. One of the more promising approaches for real-time tactile feedback uses piezoelectric actuation, which has been available in a small number of consumer devices for several years. Recently, the lack of good tactile feedback has fueled the demand for adding electrically-based tactile feedback systems.įigure 1.
.jpg)
Users are familiar with the "push to activate" feel of mechanical feedback to indicate a successful entry, for instance, on a keypad (Figure 1).
#Ultra sonic piezo actuator portable#
With the advent of touch screens replacing mechanical buttons on portable handheld consumer devices, the loss of tactile feedback has created a need for real-time feedback. This article explains the basics of piezoelectric-based actuation and how it offers a fast response time, thin profile, and low power, all of which are important in handheld applications.Ī version of this app note was published by Planet Analog in two parts, part 1 appeared on Novemand part 2 appeared on November 22, 2010. Several haptic technologies are available now, including but not limited to vibration motor actuation, piezoelectric actuation, and electro-active polymer actuation. It provides a sense of touch in a user-interface design and is the newest major interface on smartphones and other portable consumer-electronic devices. Implementing tactile (haptic) feedback in consumer-electronic devices enhances the user's experience.
